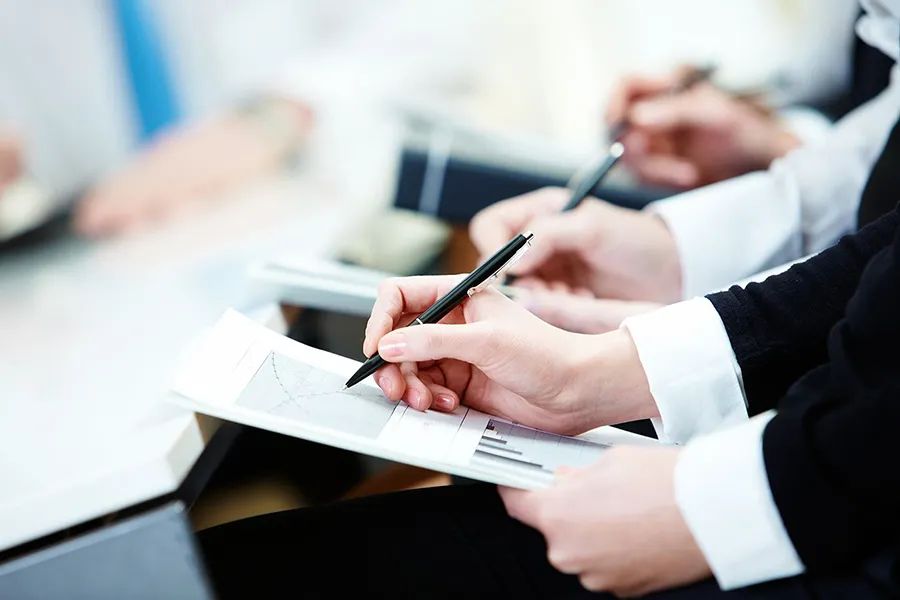
DRBFMの詳細な手法・勘所,設計品質向上と開発期間の合理的短縮を両立する手法,
問題発見と問題解決の取組み,DRBFMのワークシートの効果的な活用方法・ノウハウなど
について,豊富な経験をもとに演習を交えてわかりやすく解説する特別セミナー!!
- 講師
株式会社 ワールドテック 技術部長 山田 卓 先生 ㈱デンソーにて、車載用電子機器の設計・設計プロセス管理などに従事した後 大手企業 設計部門にて技術支援・新製品開発プロジェクトマネジメントを経て現在に至る。
- 日時
- 会場
- ※本セミナーはWEB受講のみとなります。
- 受講料
- (消費税等込み)1名:49,500円 同一セミナー同一企業同時複数人数申込みの場合 1名:44,000円
- テキスト
受講概要
受講形式
WEB受講(ライブ配信のみ) *本セミナーはZoomシステムを使用したオンラインセミナーとなります。 Zoomシステムの利用に関するお問い合わせは弊社宛メールにてお願いします。
受講対象 ・新製品設計におけるリスク対応の手法について学びたい方 ・自動車部品の設計品質について学びたい方 ・設計部門の管理者または担当者
予備知識 講義の中でも説明いたしますので必須ではありませんが、 新製品の開発プロセスに関する知識を持っていることが望ましいです。
習得知識 1)新製品の設計プロセスの完結が不確かな新規部分・変更部分・変化部分に 起因する問題の未然防止と、開発期間の短縮とを合理的に両立させるような 設計の取り組み方を理解することができます。 2)DRBFMをコアにしたチームワークによる総知・総力を注いだ問題発見と問題解決の 取組みが設計不備を未然防止するための有効手段であることを理解することができます。 3)DRBFMのワークシートの効果的な活用方法や勘所を習得することができます。
講師の言葉
新製品実現プロジェクトにおいて、リスクに対応することは必須の課題です。 さらに開発期間の短縮も求められます。それらを合理的に両立させる設計プロセスとして 推奨されているのがDRBFMです。新製品を設計しようとする際に、設計的に十分な知見を 注ぐことができず設計プロセスの完結が困難な領域が生ずることが多くあります。そこか ら生ずるリスクを未然防止するためには、問題発見と問題解決を必要十分な状態まで引き 上げることが重要です。 このセミナーでは、このような設計プロセスの良品条件が不足している新規部分・変更 部分・変化部分に対する取り組みとして工夫されたDRBFMについて学習し、DRBFMをコアに したチームの総知・総力を注いだ取り組みが設計不備を未然防止するために有効な手段で あることを理解していただきます。そしてDRBFMの詳細な手法や勘所を詳説と演習を通して 体得していただきます。 一方、DRBFMを利用した活動では、キャリーオーバー部分(即ちgood designの部分)の 設計活動とペアにしてプロジェクト活動をします。この二本立ての活動は、それぞれの活動 で処理すべき課題にフォーカスしやすくなり、設計品質の向上と開発期間の合理的短縮を両立 するうえで有効な手法となります。 DRBFMは海外でも設計活動のベストプラクティスとして特に自動車産業で推奨されています。
プログラム
1.講義「未然防止としてのDRBFM」 1.1.未然防止とは、および如何に問題を未然に防ぐのか 1.2.DRBFM早分かり 2.DRBFMの解説と演習 (2-5.から2-9.で簡単なデバイスを教材とした演習を行いながら実務の説明を行います) 2.1.未然防止の必要性 •リスクを起点に効果的・効率的に目的・目標達成を図るアプローチ(Risk-based thinking)が求められている 2.2.DRBFMの考え方、概要、有益性 •変えない部分の設計(キャリーオーバー)とDRBFMの二本立て(Dual System) •開発期間の合理的短縮と設計品質の向上の両立 2.3.DRBFMプロジェクトを完結するためのステップ •DRBFMのプロセスロードマップ •DRBFMシステムの統合 2.4.DRBFMの実施計画 •DRBFMの詳細プロセス •FMEAの5ステップアプローチ 2.5.準備 2.6.機能分析、変更点 •構造分析 •機能分析(設計の中身を見える化する) •変更・変化した部品の機能を集約 2.7.心配点、原因、影響 •故障分析(故障モードの検討、故障メカニズムの検討) •製品への影響・厳しさの検討 •専門家が参画したディスカッション 2.8.設計処置 •Preventiveな設計処置とdetectiveな検証の二元系で行う •専門家が参画したディスカッション 2.9.推奨措置 •対策の実施と効果の確認 •チームによる未然防止の保証 2.10.DRBFMを成功させるための勘所 •DRBFMの出来栄えチェック •英知を集め、協力して問題解決に導く 3.質疑応答 講師紹介 1968年 日本電装㈱(現 ㈱デンソー)に入社, 車載用電子機器の設計、車載用電子機器の設計、 設計プロセス管理などに従事 2006年-2014年 デンソー定年退職後、大手企業の設計部門にて技術支援および新製品開発のプロジェクト マネジメントの支援 2014年-2018年 その他数社に技術支援(短期間) 執筆 「機械設計」誌特集 「品質問題を未然防止するDRBFMによる設計品質の向上入門」を共著(2013年日刊工業新聞社)