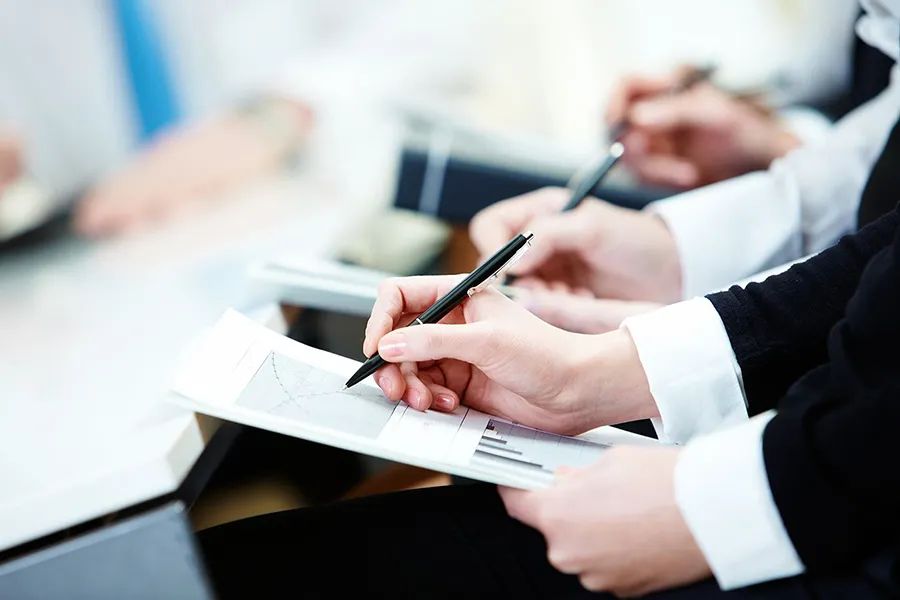
電子系のシステム設計に役立てるための
電子系向けに特化したDRBFM
(Design Review based on Failure Mode)
【WEB受講(Zoomセミナー)】※Live配信のみ、録画視聴はありません。
DRBFMの詳細な手法・勘所,設計品質向上と開発期間の合理的短縮を両立する手法,問題発見と問題解決の取組み,DRBFMのワークシートの効果的な活用方法・ノウハウなどについて,豊富な経験をもとに演習を交えてわかりやすく解説する特別セミナー!!
- 講師
株式会社 ワールドテック 技術部長 山田 卓 先生 ㈱デンソーにて、車載用電子機器の設計・設計プロセス管理などに従事した後 大手企業 設計部門にて技術支援・新製品開発プロジェクトマネジメントを経て現在に至る。
- 日時
- 2024/7/18(木) 10:00〜16:30
- 会場
- ※本セミナーはWEB受講のみとなります。
- 受講料
- (消費税率10%込)1名:49,500円 同一セミナー同一企業同時複数人数申込みの場合 1名:44,000円
※別途テキストの送付先1件につき、配送料1,210円(内税)を頂戴します。
- テキスト
- 製本資料(受講料に含む)
受講概要
受講形式 WEB受講のみへ変更となりました ※本セミナーは、Zoomシステムを利用したオンライン配信となります。 ※Live配信のみ(録画視聴はありません) 受講対象 ・電子システムの新製品設計におけるリスク対応の手法について学びたい方 ・自動車部品の設計品質について学びたい方 ・自動車部品の取引拡大・参入に関心のある設計部門の管理者または担当者 予備知識 講義の中でも説明いたしますので必須ではありませんが、新製品の開発プロセスに関する知識を持っていることが望ましいです。 習得知識 1)新製品の設計プロセスの完結が不確かな新規部分・変更部分・変化部分に起因する問題の未然防止と、 開発期間の短縮とを合理的に両立させるような設計の取り組み方を理解することができます。 2)DRBFMをコアにしたチームワークによる総知・総力を注いだ問題発見と問題解決の取組みが設計不備を防止するための有効手段であることを理解することができます。 3)電子系システムのDRBFMをアジャイル型のプロセスに取り込む方法や、DRBFMのワークシートの効果的な活用方法や勘所を習得することができます。 講師の言葉 トヨタのリーン生産方式の理念を具現化した方法はいろいろあり、それらは長期に存続しトップを走り続けるトヨタの仕事のやり方として世界中で学ばれています。その中で設計プロセスに適用されているものとしてGD3(ジーディーキューブ)があります。不備のない設計をジャストインタイムに行うにはGood Designが、そして製品の価値創造やその保証度を高めるにはGood DiscussionとGood Design Reviewが重要であるという教えです。GD3に基づく設計プロセスは、新製品実現プロジェクトにおいて求められるリスクへの対応および開発期間の短縮という課題を合理的に両立させることができます。そしてそれをサポートしているのが本セミナーで学んでいただく「DRBFM」(Design Review based on Failure Mode)です。DRBFMでは新規部分・変更部分・変化部分、即ち、現行の設計では完結させることが心配な領域にフォーカスし、その設計に不備が無いようにするために専門家を含めたチームの総智・総力を注いだ取り組みを行います。そこで行われる問題の分析や設計処置などの進め方はFMEAと同等ですが、問題の発見モレの防止や設計処置の確立を徹底的に行います。電子系システムを対象にした方法および事例を紹介いたします。 一方、新製品の設計にもキャリーオーバー部分(即ちgood designの部分)の設計活動が存在します。そのキャリーオーバーの活動とペアにしてDRBFMのプロジェクト活動をします。この2本立ての活動はそれぞれの活動で処理すべき課題にフォーカスしやすくなり、設計品質の向上と開発期間の合理的短縮を両立するうえで有効な活動方法となります。DRBFMはトヨタ自動車での取り組みから生まれ、現在では海外でも設計活動のベストプラクティスとして特に自動車産業で推奨されています。 この研修を通してDRBFMを、特に電子系のシステム設計において、有効に活用できるようになっていただきます。
プログラム
1. FMEAの復習 1.1 AIAG/VDAのFMEAの7ステップ 1.2. スコープと実施タイミング 1.3. FMEAの実施例 1.4 電子システム設計/ソフト開発とFMEA 2. 未然防止の必要性 2.1. 商品開発+新製品実現のプロジェクト 2.2. リスクに対処するための行動計画 3. DRBFMの考え方、概要、有益性 3.1. 設計プロセスの改善 3.2. 実証された設計を愚直に踏襲することが基本 3.3. 新しい設計をやる以上どこかは「変わる」 3.4. 設計における自工程完結 3.5. DRBFMの概要と有益性 3.6. 実施方法のバリエーション 4. 電子システムにおけるDRBFMの概要 4.1 電子システム設計における事前の障害防止の重要性 4.2 電子システム設計におけるDRBFMとその利点 5. アジャイル開発とFMEA/DRBFMの統合(Team FMEA/Team DRBFM) 6. 電子システム設計におけるDRBFMの方法と実装 6.1電子システム設計プロセスへのFMEA/DRBFMの統合 6.2 電子システム設計のためのDRBFM実装手順 7. 電子システム設計におけるDRBFMのケーススタディと応用 8. DRBFMの詳細実施例 8.1準備 8.2 変更点とその機能分析 8.3 心配点(故障モード)、原因、影響 8.4 設計処置 8.5 推奨処置 9. DRBFMを成功させるための勘所 9.1 DRBFMの出来栄えチェック 9.2 英知を集め、協力して問題解決に導く 10. まとめ 11. Q&A 講師紹介 略歴 ㈱デンソーにて、車載用電子機器の設計・設計プロセス管理などに従事した後、 大手企業 設計部門にて技術支援・新製品開発プロジェクトマネジメントを経て現在に至る。 執筆に「機械設計」誌特集「品質問題を未然防止するDRBFMによる設計品質向上入門」を共著(2013年 日刊工業新聞社)。
関連セミナー
05/17(金)
終了済みオープンセミナー
加速試験の成り立ちと各種事例に基づく実践的な加速係数の求め方 ~市場条件に適合する試験条件、加速理論に裏付けられた試験法へのステップアップ~ 【会場/WEB選択可】WEB:ライブ配信/アーカイブ配信(7日間、何度でも視聴可)
06/07(金)
終了済みオープンセミナー
未然防止のためにFTAを効率的に使いこなすポイント ~FMEAやDRBFMとの関係性・使い分けと実践~【会場/WEB選択可】WEB:ライブ配信/アーカイブ配信(7日間、何度でも視聴可)
03/19(水)
終了済みオープンセミナー
半導体・回路素子・電子部品における劣化寿命の故障モード・因子とその故障の寿命点 【会場/WEB選択可】WEB:ライブ配信/アーカイブ配信(7日間、何度でも視聴可) ※個別質問受付可能
07/30(火)
終了済みオープンセミナー