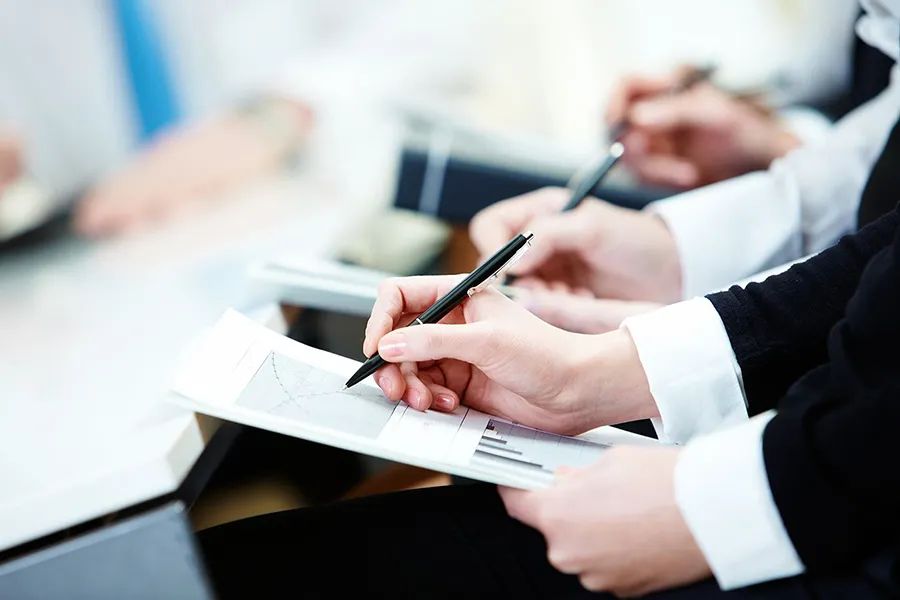
10年周期で繰り返されるはんだトラブル。その根因と真理を、技術の語り部が徹底解説。進化する実装技術を実務で使いこなすための“知の再構築”を習得できます。
鉛フリー・極小チップ・両面実装・還元はんだ・誘電はんだなど、進化の裏に潜むリスクと対策を学べる特別セミナー!!900ページ超のテキストは、事典としても活用できます。
- 講師
技術コンサルタント 伊藤 千秋 先生
オムロン株式会社 品質保証部長,部品技術部長等歴任後現職 制御機構部品の品質保証を15年,自動車電装部品の品質保証23年経験,
品質・信頼性一筋のプロフェッショナル この間,日本科学技術連盟 信頼性開発技術研究会 委員長などを歴任
- 日時
- 2025/9/26(金) 10:00〜16:50
- 会場
- 受講料
(消費税率10%込)1名:49,500円 同一セミナー同一企業同時複数人数申込みの場合 1名:44,000円
※製本テキストを購入される場合、資料:11,000円(税込)+別途テキストの送付先1件につき配送料1,210円(税込)を頂戴します。
- テキスト
- PDF資料(受講料に含む)
受講概要
- 受講形式
会場・WEB
- 受講対象
実装設計・製造技術・品質保証・クレーム処理・生産技術・実装設備に関わる技術者
- 予備知識
特に必要ありません。
- 習得知識
1)はんだ付け技術の過去から現在までの技術の変遷の歴史を知ることができる
2)新旧はんだ付け技術ならびにその周辺技術のおさえどころを学ぶことができる
・はんだ接続のメカニズム
・はんだ実装材料の選定の基本
・リフローはんだ実装の特性,信頼性,故障モード
・フローはんだ実装の特性,信頼性,故障モード ・両面実装の特性,故障モード
・はんだ接続の寿命予測
3)豊富な技術データ・画像データを手に入れることができる
- 講師の言葉
はんだ付けは古来より実施されてきている接合法であるが、慣れ親しんでいる工法である割には過去よりなんどもトラブルを引き起こしている古くて新しい技術の一つである。
自動車では鋼鉄の車両の中に閉じ込められているユニットが受けるストレスはとくに大きく、周囲温度・自己発熱による熱耐久寿命、雨水や結露によるリーク劣化寿命、静荷重によるクリープ寿命などのトラブルが経験事例として豊富に蓄積されている業界・用途でもある。
近来ではこれに鉛フリーはんだ、金属基板実装、両面実装、フリップチップ実装で始まった技術が、極小チップ部品、BGA実装、フレキシブル基板実装、フラックスレス実装などとして大幅な技術の進歩がみられている反面、還元リフロー、誘電はんだなどの新しい技術も出てきている。
こうした中、過去に経験したトラブルが繰り返し起こってきているのも事実である。これはほぼ10年を区切りに技術者の世代が変っていくためとみられ、伝承が十分でないということでもある。
はんだ実装の技術にはその核心となる技術については古き時代からの普遍的な理論、経験則があり、それを引き継ぎながら世代が変わるごとに失敗を繰り返すようなことがあってはならないのである。この講座は講師の長年の自動車電装部品に携わってきた経験から「技術の語り部」として余すところなくお話する。
- テキストに関して
本セミナーのテキストは、PDFテキストの配布となりますが、製本版のテキストを購入いただくことも可能です。
写真付きで、豊富な事例がリストアップされています。
製本テキスト資料:11,000円(税込)
※購入希望の方は、お申込み時に備考欄に「製本テキスト購入希望」と記載してください。
- 受講者の声
おさえるべき要点を尽くしてくれる解説でわかり易かった。社内の問題についても質問させていただき、貴重な意見を戴いたので早速社内に展開したい。テキストの事例集が大変参考になります。
基本的な部分の説明からでわかり易かった。普段何気なく用いている手法がどういった背景で用いられるようになったのかが理解できた。
はんだや基板、フラックスなどの実装材料の組成の基本的な成り立ちがよくわかった。
自分の実務担当外の普段関わり合いのない工法や検査に至る幅広い話が聞けて良かった。実例だけでなく理論についても触れられておりとてもわかり易かった。
非常に実践的で試験結果や検討データに基づいた講義で理解が深まりました。 今まで理由がわからずに引き継いできた知識を具体的な事例や数値で知ることができました。
プログラム
1.はんだ実装技術の変遷と確立された技術、廃れた技術
(1)はんだ材・フラックス材・積層板の変遷
(2)実装工法の変遷
(3)フローはんだの変遷
(4)リフローはんだの変遷
2.接合構造
(1)はんだ接続構造(拡散層・金属間化合物)
(2)はんだ接合のメカニズム(フラックス反応・はんだ溶解・はんだ流動・はんだ凝固)
(3)はんだ合金層(β層・ε層・η層・γ層)
(4)はんだ接合面の空孔(カーケンダルボイド)
3.実装材選定の考え方
(1)はんだ(構成元素ごとの機能役割と共焦点・融点・軟化点・脆化点)
(2)フラックス(固形樹脂・活性剤・溶剤・pHとpka・融点・沸点が濡れ性に与える影響)
(3)積層板(PP材・CEM材・GE材・FPC材とTg点・線膨張係数が膨張収縮に与える影響)
(4)ガラスクロス(層数・組数・ピッチが膨張収縮に与える影響)
(5)シランカップリング処理(ガラスクロスとの接着性・疎水性の影響)
(6)銅箔(電解銅箔・圧延銅箔と伸び性・繰返曲げ強度に与える影響)
(7)スルーホール面粗さ(一般仕様・特別仕様)
(8)めっき厚み(一般仕様・厚めっき仕様)
(9)基板めっき(パネルめっき・パターンめっき)
(10)めっきを厚く形成できるめっきとパターン精度よくできるめっき
(11)高アスペクト比のホールを形成するめっき
(12)追従性の良いめっきとレベリング性の良いめっき
(13)故障モードとその対策
4.表面実装
(1)工法(大気・窒素・真空/平行流・垂直流・垂直乱流)
(2)加熱制御(スリットノズル・管ノズル)
(3)冷却制御
(4)はんだペースト(樹脂・活性剤・溶剤)
(5)フロントフィレット・バックフィレット・はんだ浮き高さがはんだ剪断強度へ与える影響
(6)実装部品のリードフレームの断面がはんだボールへ与える影響
(7)側面電極・底面電極とはんだボールへ与える影響
(8)はんだ粒の溶解と結合のメカニズム
(9)温度プロファイルの主要点の考え方
(10)メタルマスク
(11)はんだ転写率(面積比・体積比)制御
(12)版離れ制御
(13)故障モードとその対策
5.挿入実装
(1)工法(大気・窒素・真空/噴流はんだ・部分はんだ・混載はんだ)
(2)一次噴流(バックフロー・はんだ圧力・液面高さ)
(3)二次噴流(ゼロ速度・平坦浸漬・離脱角)
(4)フラックス塗布制御
(5)ポストフラックスのはんだプロセスでの各ポイントでの機能役割
(6)温度プロファイルの主要点の考え方
(7)進入角度制御(流し方向・はんだ液面高さ)
(8)クリアランス制御(基板穴形状・径)
(9)ドロス制御(突沸現象)
(10)故障モードとその対策
6.両面実装
(1)両面実装の各種方式(混載実装・マスク実装・両面リフロー実装)
(2)両面実装の規制条件
(3)はんだ軟化温度(最高許容温度)
(4)再加熱によるウィッキング・低融点成分偏析・凝固・はんだ剥離のメカニズム
(5)ポイントフローはんだ・ポイントディップはんだ・マスキングフローはんだ
(6)故障モードとその対策
7.極小チップ部品実装
(1)チップ部品(外形精度・電極精度・キャリアテープ)
(2)基板(パタン精度・エッチング精度・サイドエッジ)
(3)チップマウント(位置精度)
(4)はんだペースト(微細粒はんだ)
(5)フラックスレス実装
(6)基板レス実装
(7)故障モードとその対策
8.フレキシブル基板実装
(1)フィルム材・銅箔材
(2)低融点はんだ
(3)チップオンフィルム実装
(4)故障モードとその対策
9.バンプ実装
(1)実装方式の変遷
(2)フリップチップ実装
(3)はんだバンプ形成法(はんだボール・めっき・スパッタリング・レジストフィルム)
(4)故障モードとその対策
10.コテはんだ付け
(1)各種方式(手はんだ・ロボットはんだ)
(2)熱変換効率
(3)故障モードとその対策
11.レーザはんだ付け
(1)焦点径、焦点距離
(2)反射率
(3)故障モードとその対策
12.還元リフロー
(1)工法(水素還元リフロー・蟻酸還元リフロー)
(2)フラックスレス還元はんだのメカニズム
(3)温度プロファイル
13. 誘電はんだ付け
(1)高周波誘電加熱と高周波誘導加熱
(2)誘導加熱はんだメカニズム
(3)温度プロファイル
(4)表皮効果・近接効果
14.はんだ印刷画像検査(SPI)
(1)検査工法(2次元測定・3次元測定)
(2)分解能と検出領域
15.多数個取り基板の基板分割
(1)工法(ルータ加工・回転刃加工・押切刃加工・プレス加工・手割加工)
(2)工法ごとの基板分割時のひずみの大きさ
(3)故障モードとその対策
16.はんだ付け画像検査(AOI)
(1)検査工法
(2)分解能
(3)故障を引き起こすアーク、バーストノイズとその対策
17.X線画像検査装置(AXI)
(1)検査工法
(2)BGAボイド画像検査・BGA変形画像検査
18.インサーキットテスト・ファンクションテスト
(1)工法
(2)動作シーケンス
(3)プローブピン・フィクスチャ
(4)過電圧破壊を起こすバーストノイズ
質疑・応答
略歴
社歴
昭和無線工業(現SMK):5年2ヶ月
トリオ(現JVCケンウッド):3ヶ月
立石電機(現オムロン):38年7ヶ月
職歴
スイッチ製造技術:3年2ヶ月
コネクタ製造技術:1年
圧着・ハーネス製造技術:2年
アンプ・チューナ製造技術:3ヶ月
部品メーカ監査(加工部品):20年 (電子部品・機構部品):25年 制御機構部品(リレー・スイッチ・タイマ・センサ)品質保証 :15年
自動車電装部品(ECU・リレー・センサ・スイッチ)品質保証 :25年
最終職位
品質保証部並びに部品技術部 部長 韓国オムロン電装 理事(役員) 上海欧姆龍控制電器 顧問 福達合金材料 顧問
学会活動
日本信頼性学会会員:23年
日本信頼性学会企画委員(地域委員):2年
日本科学技術連盟講師:24年 日
本科学技術連盟信頼性開発技術研究会 委員長:2年(1期)
日本科学技術連盟信頼性開発技術研究会 副委員長:4年(2期)