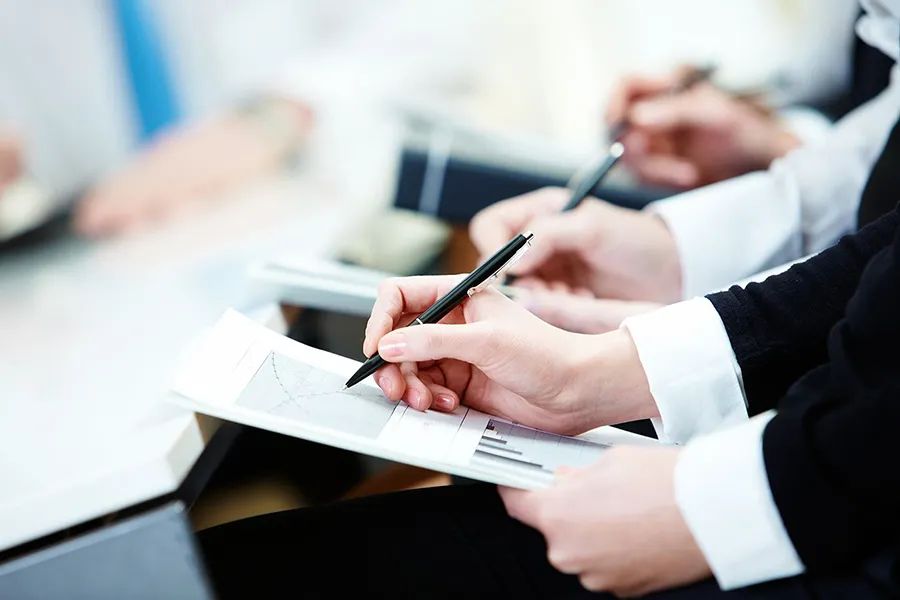
接着の長期信頼保証のための
接着劣化のメカニズムと評価のポイント、長期寿命予測法、設計基準、
安全率の定量化法および耐久性のトラブル事例(実践編)
接着劣化のメカニズムと評価のポイント、長期寿命予測法、設計基準(設計法)、安全率の定量化法および
耐久性のトラブル事例を解説する13年間の実績を有する特別セミナー!!
- 講師
(株)原賀接着技術コンサルタント
専務取締役 首席コンサルタント 工学博士 原賀 康介先生
三菱電機(株)研究所にて入社以来接着接合技術の研究・開発に従事,主席技師長等を経て2012年退職,独立。
40年間機器組立に接着剤を活用し高信頼性接着技術を構築してきた接着の耐久・信頼性の第一人者
- 日時
- 会場
- 受講料
- 1名:48,600円 同時複数人数申込みの場合 1名:43,200円
- テキスト
受講概要
4月21日接着(基礎編)セミナーと併せて同じ人が2日間受講の場合
受講料(消費税等込) 1名:74,520円 同時複数人数申込みの場合 1名:66,960円 http://thplan-test.uh-oh.jp/seminars/8149/ の「→ お申し込みページへ」からお申込み下さい
受講対象
接着に関する基礎的知識をお持ちで、耐久性で困っておられる技術者
習得知識
1)劣化のメカニズム
2)耐久性評価試験のポイント
3)長期耐久性の寿命予測法
4)高信頼性接着の設計基準(設計法)
5)耐用年数経過後の安全率の定量化法
講師の言葉
接着接合は部品組立における重要な要素技術であるが、長期耐久性を正確に予測する方法は確立されておらず、 接着接合を製品に適用する際、「何年もつか」ということが常に議論される。「実際に使ってみなければわからない」と いうあいまいな状態で接着接合を採用するわけにはいかない。接着接合物の安全性、信頼性を保障できるデータ的な 「裏付け」としっかりとしたストーリーが必要である。 講師はまさに接着接合を製品に適用するための安全性、信頼性の「裏付け屋」的立場で、これまでに各種の環境や 応力に対する耐久性評価や長期耐久性予測、耐久性を向上させるための方法について検討し、これらの蓄積をベースとして 接着の信頼性保証ストーリーを構築してきた接着の耐久性、信頼性の第 一人者である。 本セミナーでは、接着接合物の長期信頼性保証のために必要な、劣化のメカニズムと評価のポイント、長期接着耐久性の 寿命予測法、ばらつきや劣化、内部破壊などを考慮して簡易に必要な初期の平均強度を見積もる設計法(原賀式CV接着設計法)、 最適設計を行うための耐用年数経過後の安全率の尤度の定量化法を、講師がこれまでに行ってきた豊富なデータに基づいて わかりやすく紹介するとともに、信頼性、耐久性、寿命、安全率に関連するトラブル事例を説明します。 このセミナーは、13年間にわたって、一貫して「接着不良の未然防止と接着信頼性の向上」を目的としてきた「接着剤を使う 立場」からの他に類のないセミナーで、モノづくりに接着を使用する機器製造企業の技術者は勿論、接着剤メーカーの技術者にも 好評を博してきました。 テキストの他に、解説図書として「高信頼性を引き出す接着設計技術-基礎から耐久性、寿命、安全率評価まで-(日刊工業 新聞社刊)」を配布します。 今回は「自動車軽量化のための接着接合入門」も配布(1日間受講でも2日間受講でも一人一冊)いたします。 書籍がご不要な場合でも割引はご容赦願います。
プログラム
1.接着劣化のメカニズムと評価のポイント (1)劣化の要因とメカニズム ①接着接合物の劣化箇所 ②接着接合物の劣化を生じさせる外的要因 ③劣化のメカニズム 熱劣化 ヒートサイクル、ヒートショック 水分による劣化 継続荷重(クリープ) (2)耐久性評価の落とし穴 ①水分劣化における接着部の形状・寸法の影響 接着面積/外周の長さと水分劣化の関係 ②細長い接着部における幅の影響 接着部の幅と水分劣化の加速倍率 ③吸水後の乾燥による接着強度の回復(乾燥可逆性) ④クリープ耐久性に及ぼす水分の影響-応力と水分の複合劣化- ⑤疲労試験における注意点 (3)耐久性の相対評価試験、絶対評価試験、規格評価試験 (4)絶対評価試験における加速評価条件の最適化 ①ヒートサイクル試験の条件最適化 年サイクル試験と日サイクル試験の分離 接着剤の内部応力と温度との関係 ②熱劣化試験の条件最適化
2.接着耐久性の長期寿命予測法 (1)寿命予測の鉄則 (2)長期熱劣化の予測法 ①アレニウス法 ②アレニウス法による熱劣化の予測法 (3)長期水分劣化の予測法 ①アレニウス法による予測法 ②吸水率分布からの有限要素法による予測法 ③飽和吸水率、拡散係数の求め方 (4)長期屋外暴露劣化の予測法 ①アレニウス法と乾燥回復性を考慮した予測法 ②予測と実験結果の比較 (5)クリープ耐久性の予測法 ①応力負荷装置 ②温度・時間換算による予測法 ③Larson-Millerのマスターカーブ法 (6)疲労耐久性の予測法
3.接着の設計基準-原賀式 『CV接着設計法』- (1)原賀式『CV接着設計法』 とは ①目標とする工程能力指数を満たし、下側規格値を満足するためには、変動係数CVをどの程度にすべきかを容易に算出する。 ②劣化や内部破壊を考慮して、接着部に作用する力に対して、接着部の初期の平均接着強度は何倍確保すべきかを、容易に求める。 (2)ばらつきと分布の形、許容不良率 (3)「不良率(破壊確率)」と接着強度のばらつき (4)許容不良率の上限強度と 接着強度のばらつき(変動係数CV)の関係 (5)「品質」に関する基準「工程能力指数」 ①下側規格値はどのくらいに設定すれば安定した品質と言えるのか? ②過剰な不合格品を出さないためには、接着強度のばらつきをどのくらいに押えれば良いのか? ③許容不良率、工程能力指数、変動係数、下側規格値/平均値の関係、 (6)劣化による強度低下とばらつきの増加 ①初期の平均強度は、最大負荷力の何倍有れば良いか? ②劣化後保持率、下側規格値と最低限必要な初期平均値の関係 (7)内部破壊を考慮した構造設計上必要な平均強度は最大負荷力の何倍か? (8)設計式 ①工程能力指数、下側規格値から必要な初期の変動係数を求める式 ②劣化を考慮して最大負荷力に対して必要な初期平均強度の倍率を求める設計式 ③劣化、内部破壊と安全率を考慮して、最大負荷力に対して必要な初期平均強度の倍率を求める設計式
4.最適設計のための製品の耐用年数経過後の安全率の尤度の定量評価法(改良法) (1)この評価法の適用の目的と前提条件 (2)接着強度の経年変化の概念 (3)耐用年数経過後の安全率の算出法 ①評価のプロセス ②疲労やクリープなどが加わる場合 ③一時的な静荷重だけが加わる場合 ④耐用年数経過後のばらつき係数の求め方 ⑤耐用年数経過後の複合環境劣化係数の求め方 (4)耐用年数経過後の安全率の算出事例 ①接着部の要求条件と評価条件への落とし込み ②高温疲労試験から基準強度を求める ③静的強度試験から耐用年数経過後のばらつき係数を求める ④年サイクルヒートサイクル試験の劣化係数を求める ⑤日サイクルヒートサイクル試験の劣化係数を求める ⑥熱劣化試験の劣化係数を求める ⑦実効接着強度を求める ⑧耐用年数経過後の安全率の尤度を求める (5)安全率の尤度の再配分 ①許容不良率の低減への配分 ②接着作業性の改善への配分
5.信頼性、耐久性、寿命、安全率のトラブル事例 ①出荷品の性能、条件、②トラブルの状況、③当初の判断、④検証抜けの要因、⑤追加検証の結果、⑥原因の推定、⑦不良率の推定、⑧対策、⑨対策品の信頼性推定、などを説明 (1)ばらつきを考慮せず平均値で設計した (2)乾燥による強度回復性を考慮しないで接着剤を選定した (3)クリープが加わっている状態に気がつかなかった (4)試験片と製品の接着部の形状・寸法の違いを考慮しなかった (5)疲労強度を間違った (6)引張り剪断試験で結果を見誤った など