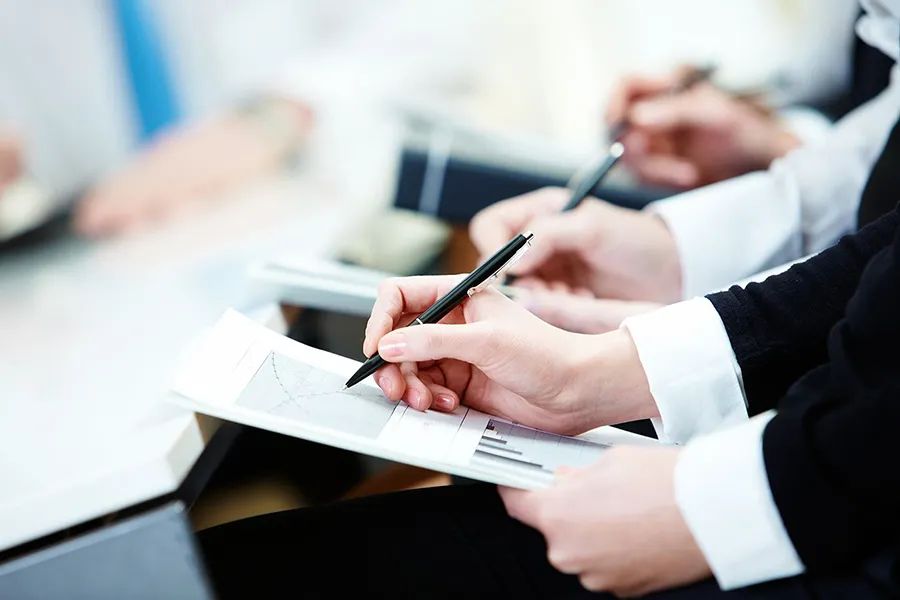
設計上のノウハウを理解し,活用するための
若手設計者の短期戦力化に必要な設計経験則修得の上手な進め方
設計上のノウハウである設計の経験則について根拠,知らない場合の問題点,
活用した場合の効果などケーススタディを通して具体的に解説する特別セミナー!!
- 講師
伊豫部技術士事務所 所長 伊豫部 将三先生
富士重工業(株)に17年間勤務の後独立,150社以上で設計技術部門の業務改善の支援に従事
- 日時
- 会場
- 受講料
- 1名:48,600円 同時複数人数申込みの場合 1名:43,200円
*中小企業従業員で、事前の申請が中小企業庁に認可採択されると、
受講料等費用の2/3が補助されるセミナーです
- テキスト
受講概要
予備知識
特になし
セミナーのポイント
1)部品材料選択の基準・基本 2)材料強度と混入成分の影響 3)材料強度と熱処理の影響 4)材料強度と環境温度の影響 5)腐食防止と材料の関連 6)部品間嵌め合いと最適隙間 7)部品寿命と熱・環境温度の影響 8)部品摩耗と面圧・速度の影響 9)疲れ強さと衝撃強さの相関 10)成形加工と材料選択の基本・他
補助金対象講座
このセミナーは中小企業庁の「ものづくり小規模事業者等人材育成事業」の指定講座につき、
中小企業の方には受講料の2/3,交通費の2/3,宿泊費の2/3の補助金が支給されます。
詳細は下記URLにてご確認願います。
指定講習会受講希望者の方へ
事務局ホームページ
http://www.mstc.or.jp/jinzai/jyuko.html
(一財)製造科学技術センター ものづくり人材育成事業部 TEL. 03-3500-4891
※)中小企業庁の「ものづくり小規模事業者等人材育成事業」の指定講座の受講に関する補助金申請受付けは、
中小企業庁により9月17日で締め切られました。
受講のお勧め
設計の経験則とは、機械・電気・化学・建設分野などの商品・製品・装置・部品の開発・設計・生産準備・製造・施工・ 保全・運用を通し、それぞれの企業の担当者が、毎日の仕事の中で、苦労して思考錯誤と試行錯誤しながら積み上げ 蓄積したノウホワイ(Know-Why)と、ノウハウ(Know-How)部分のことを言います。 ここでノウホワイ(Know-Why)とは、商品・製品・装置・部品へ作り込みが要求される機能(用途・目的・働き)を 実現するために、物理法則・工学上の効果などの現象を、如何に的確に役立つ様に、原理・方式・構造・材料・処理・ 形状組合せなどを選択する部分を言います。 またノウハウ(Know-How)とは、選択した原理・方式・構造・材料を、顧客が満足する商品・製品・装置・部品・要素機能を 実現しながら、安全性・寿命・信頼度・精度品質・目標コストを如何に実現するか、の組合せ法選択部分である。 前述の商品・製品・装置・部品開発・設計取り組み時に、先輩技術者が永い時間と経験で築き上げたノウホワイ(Know-Why)と ノウハウ(Know-How)である経験則の活用がコストダウン・短納期・高機能・高品質確保に役立つ。特に新人層の短期戦力化と 未熟なベテラン層の習熟度を一層高め、設計品質を高める上で同時に大切となる。 これら経験則を社内教育で事前修得実施が適切・充分に実施出来ない場合には、教育不備を補う手順書・基準書・ 手本図・標準図・等の技術資料類整備と活用義務付け、また教育と技術資料不足部分を上司・先輩・チームリーダーによる 着手時の事前注意点指導も適切実施ができず不備・不足・欠如がある場合には、DR0(基本仕様・構想設計立案法指導と 事前確認).DR1(開発・新規着手部分の故障予測と事前検証で基本設計法指導と事前確認),DR2(工法・精度・ コスト選択組合せ詳細設計法指導と事前確認),出図用図書作成(図面作成法指導と事前確認)時の不備・不足・欠如で 手戻り・手直し時間の24%(DR部分が16%で、出図前検図部分が8%)が発生、出図後の製造と購買部門経由取引先からの 製造クレームで手戻り・手直しによる図書差し替えで手戻り時間の23%が発生、立会・検収時客先指摘で手戻り・手直し (追加の出図と購入・製作再手配)で手戻り時間の8%が発生、出荷後の市場・客先クレームによる手戻り・手直し (不具合対策措置)で手戻り時間の45%が発生等で、納期遅れやコストアップを繰り返す結果になります。 前記設計不良による後始末としての手戻り・手直しで設計部門全体の消失時間は多くの企業で合計30%に及び、 直接クレームによる損失金額は売上の2%を超え、開発・設計原因が70%を占める各社共通実態があります。 これらの大部分は、入社3年以内の新人と教育不備・等による未熟なベテラン(入社6年前後まで)の人達によって 発生させている現実があります。 前記損失を少しでも軽減したいと望む場合には、新人層と未熟なベテラン層へ上司・先輩・チームリーダーによる 過去に築きあげた経験則教育の充実・強化が特に大切になります。また新人層の短期戦力化と未熟なベテラン層の 短期習熟度向上化を進め、設計品質の向上を押し進める上でも大きな役割を果たします。 本セミナーでは、新人設計者にも判り易く修得できる様に101テーマのケーススタディで、①・経験則の根拠、 ②・知らない場合の問題点、③・適用・応用上の注意点、④・活用した場合の効果、などの説明・紹介を通し、新人層と 未熟なベテラン層および教育担当者、チームリーダーが是非知って置かなければならない内容を、具体的に分かり易く 説明・指導致します。
プログラム
Ⅰ・商品設計に必要な経験則101
1・10度C温度上昇寿命半減則 2・嵌め合い隙間1/5000最適則 3・機械的性質向上調質有効則 4・硬さ向上C増加有効則 5・機械的性質焼き戻し温度支配則 6・硬さ対疲れの比18則 7・引っ張り対比45則 8・焼き入れ度合い対降伏比逆比則 9・疲れ強さ最大HRC45則 10・高温時機械的性質温度影響則 11・切り欠き0・5㎜疲れ半減則 12・低温時引っ張り強さ増加則 13・切り欠き部材の焼き戻し温度と疲れ関連則 14・結晶粒対疲れ強さ(疲労限)逆比則 15・耐疲労表面仕上げ有効則 16・腐食下の疲れ無抵抗則 17・耐衝撃確保C0・7以上回避則 18・焼き入れ度対衝撃比例則 19・―60度C耐衝撃無抵抗則 20・中圧・中速接触時の耐摩耗C0・9選択則 21・高圧・低速接触時の耐摩耗C0・9回避則 22・切り欠き靱性合金元素影響則 23・低温時の耐衝撃確保ステンレス有効則 24・耐食性確保ステンレス有効則 25・ステンレスの降伏比向上加工度有効則 26・Al材の疲れ強さ(疲労限)材種無関係則 27・黄銅の機械的性質加工率影響則 28・Al青銅の機械的性質Al%影響則 29・鋼板の限界絞り比2以下確保則 30・プレス打ち抜き剪断抗張力確保則 31・抜き穴・外形精度クリアランス影響則 32・箱曲げ角隅割止め穴必然則 33・板材曲げ加工時の反り必然則 34・抜き穴間隔最小2倍則 35・V曲げ時の精度確保コイニング選択則 36・V曲げ時の伸び代曲げ角度影響則 37・シャー剪断時の直角度シャー角支配則 38・打ち抜き品の穴抜きばり逆向き則 39・絞り品の表面積ブランク面積同一則 40・加工時硬化材種毎のn値(加工硬化係数)支配則 41・絞り品の置き割れ残留応力影響則 42・Al管の最小曲げ半径肉厚比例則 43・絞り型空気抜き必然則 44・プレス時の安全確保無人化必然則 45・十字隅肉溶接強度70%則 46・突き合わせ継ぎ手開先1/2確保則 47・溶接熱影響部衝撃低下則 48・溶接熱影響部引っ張り強さ向上則 49・溶接割れ防止予熱と応力除去焼鈍必然則 50・溶接熱影響回避則 前記を含め著書「設計の経験則101」と「続・設計の経験則101」を含め合計202項目の経験則をご紹介いたします。