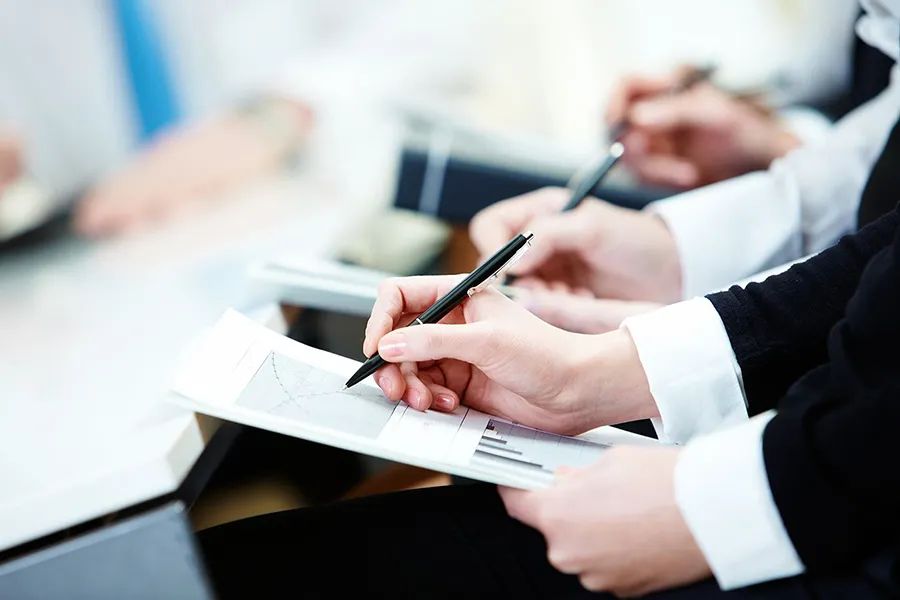
一般理論を理解し,実務で役立てるための
車載電装部品の信頼性加速試験・寿命予測と設計品質保証
加速係数の求め方,寿命予測のやり方の実務的な進め方および
信頼性目標クリアの試験評価や設計目標達成の仕組みについて実務経験を踏まえて解説する特別セミナー!!
- 講師
オムロン(上海) 顧問 伊藤 千秋先生
オムロン株式会社 品質保証部長,部品技術部長歴任後現職
制御機構部品の品質保証を15年,自動車電装部品の品質保証23年を含めて品質・信頼性一筋のプロフェッショナル
- 日時
- 会場
- 受講料
- 1名:47,250円 同時複数人数申込みの場合 1名:42,000円
- テキスト
受講概要
予備知識
信頼性試験や品質保証に携わっている方なら特になし
習得知識
加速試験の理論、実務知識やそのすすめかた、試験法に対する成り立ちや加速係数等の試験法への反映のしかた
受講対象者
設計および設計評価の仕事に携わる人 市場クレームなどの品質トラブルの解析・分析・処理の仕事に携わる人
受講者の資格要件
故障解析や信頼性のデータ解析(ワイブルや累積ハザード解析など)を理解されている人
講師の言葉
われわれの日々の製品・部品の評価のために用いられる試験法は本来的にいえば市場条件を反映したもので あるはずであるし、製品のライフに相当する回数・時間で設定され、その加速条件で試験法ができているはずで ある。 ところが、試験法の根拠・拠所を求めるあまり、公的規格や業界規格にこだわりすぎた所があったりした きらいがあって、ともすれば市場や使用の条件とずれ加減のところが時としてクレームとして現れてくることが ある。 この講座は加速試験とはなにか、加速係数のもとめかた、その加速係数を基に実験室データから寿命予測を したり、市場回収品を基に余寿命予測をするやりかたを解説していく。 また、既存の試験法の成り立ちを見直して、もともと設定している寿命や条件に対してあっているのかどうかを 考えてもらう場として考えている。 加速をとらえていくのに、従来は理論式が中心のアプローチで実際の 市場データとの差があってやりかたの上で詰まっていたり、市場データがきっちりと取れない市場の中でどう 考えていったらいいのか壁にぶち当たって一向に進まない、そんな現実にぶち当たっているかたも多い。 この講座では一般理論を理解したうえで、より実務的なすすめかたを事例として紹介して次なるステップを 切り開く場としていきたい。 さらに、この加速の理屈を理解したうえで自動車部品に要求される信頼性目標と その目標をクリアしているかどうかを見定める試験・評価や設計目標を達成するための体制や仕組みについて 紹介していく。
プログラム
第1章 故障モデルと加速試験
(1)加速試験とは (2)加速試験の成り立つ条件と制約条件 (3)加速試験の拠所となる故障モデル (4)加速試験の種類と考えかた (5)加速試験と寿命予測のやりかた (6)実施事例 a.マグネットワイヤの耐湿寿命(市場データと試験データから) b.マグネットワイヤの耐湿寿命(アイリングモデルから) c.はんだ熱疲労寿命(市場データと試験データから) d.はんだ熱疲労寿命(試験完了品の組織粗大化ダメージ度から) e.はんだ熱疲労寿命(はんだ材SN図から) f.はんだ熱疲労寿命(Coffin-Mansonの式から) g.プリント基板の結露サイクル寿命(結露サイクル試験と滴水試験から) h.近接センサの温冷浴寿命(田口メソッドから) i.ポリアセタール樹脂の耐熱寿命(アレニウス則から) j.マグネットワイヤの耐熱寿命(アレニウス則から) k.振動疲労寿命(6.5乗則から) l.ゴム劣化寿命(回収品ダメージ比較法および類似品比較法から) m.ゴム封止寿命(実験データから) n.ゴム劣化寿命(材料別にアレニウス則から) (7)加速係数の実用試験への展開 a.高温・低温・温度変化 b.湿度・湿度変化 c.振動・衝撃 d.電圧・電圧変動 e.ノイズ・サージ f.動作繰り返し (8)加速データを求めるための数々の試み (9)材料別故障モデル式 a.金属(腐食・疲労・摩耗・酸化・硫化など) b.ゴム(酸化劣化・オゾン劣化・接触劣化など) c.プラスチック樹脂(熱劣化・湿度劣化・紫外線劣化・マイグレーションなど) d.コイル・モータ(熱劣化・耐湿劣化・複合劣化など) e.半導体(電圧劣化・高温劣化・湿度劣化・熱疲労など)
第2章 設計の品質保証
(1)重要・保安部品の定義と区分 (2)業界からの信頼性要求の水準 (3)設計上の押えどころ a.部品の故障が車両に与える影響度とその故障モードの定義 b.致命・重故鐘のFTA(シングルフェイラーポイントの対応・グレーゾーンの検証) c.長寿命設計と死にざま設計(特性保証・動作保証。故障モード保証) d.部品選定(自動車部品としての適合度の評価) e.ディレーティング(負荷軽減) f.設計FMEA(設計検証と対策によるレイティング切り下げ) g.設計評価(変化点検証・新部品検証・過去トラ検証・限界検証・実車検証・全バラ検証) (4)ライン管理点への展開