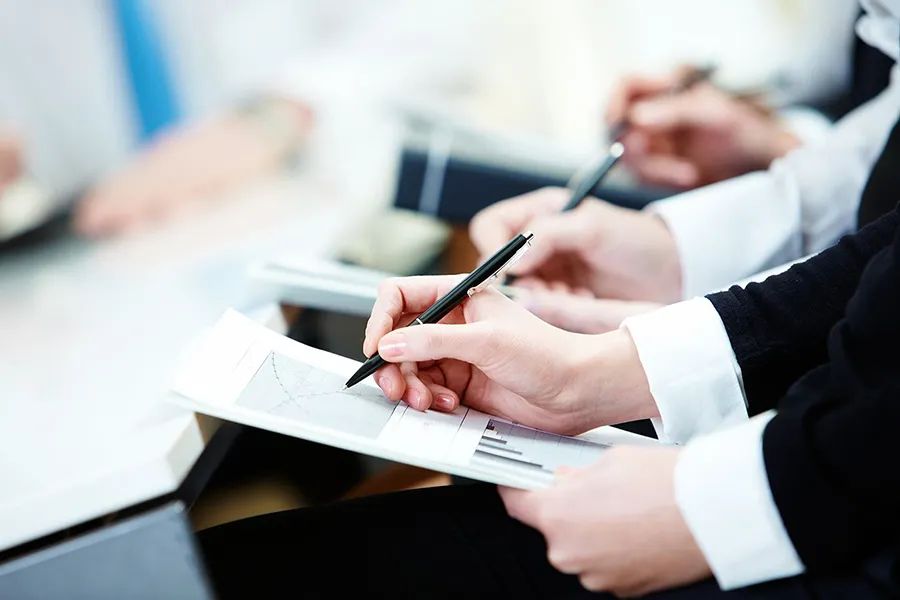
設計品質を確保し,クレーム予防にDRを本当に活用するための
設計着手時からクレーム予防できるDR(デザインレビュー=設計審査)の上手な進め方
(DRツール作成演習付き1日講座)
クレーム予防のためのデザインレビューの効果的取組み方法について
事例を交えて具体的に解説する特別セミナー!!
- 講師
伊豫部技術士事務所 所長 技術士(機械部門) 伊豫部 将三先生
富士重工業(株)に17年間勤務後、100社以上の各種製造企業にて開発・設計・生産部門の業務支援に従事
著書:「設計の凡ミス退治101」「設計の故障解析51」「設計審査(DR)支援ツール集・Ⅰ」(何れも日刊工業新聞社刊)など多数
- 日時
- 会場
- 受講料
- 1名:47,250円 同時複数人数申込みの場合 1名:42,000円
- テキスト
受講概要
受講対象者
DRを本当に活用したいと考えている開発・設計・品質保証部門のリーダー,管理,監督者の方
予備知識
デザインレビューに関心のある方なら特になし
習得知識
1)開発・設計時の評価・判定・検証法の原則,基準ルール 2)開発・設計部門以外のデザインレビューへの関わり方 3)クレーム防止に役立つDRツールとしての基本仕様書・故障解析表の活用方法 4)クレーム未然防止に必要なデザインレビューの実施方法
その他
故障予測対策できる設計の故障解析51事例入りCD-ROMを配布
講師の言葉
DR(設計審査))とは本来、設計品質を確保しつつクレームを未然に防ぎ、手戻り削減とコストダウンを行う ために行われる非常に意義あるものです。しかし多くの技術部門ではクレームの多発に悩み、併せてDR・ 検図時の手戻り、出図後の製造・取引先からの手戻り、出荷前立会時の手戻り、納品・検収後客先からの クレームに伴う手戻り等で、講師調査では技術部門が投入する時間の30%が失われている実態があります。 前記手戻り時間の中味では、24%がDRと検図時の手戻りで、出図後の製造と取引先からの手戻りは23%、 出荷前立会時の手戻りは8%、納品・検収後客先からのクレームに伴う手戻りは45%です。前記客先から クレームに伴う手戻りは検収1ケ月以内が25%、3ケ月以内が13%、6ケ月以内が11%、1ケ年以内が21% 3ケ年以内が19%、6ケ年以内が6%、10年以内が4%、10年以上経過するものも1%の実態があります。 手戻りを発生原因別に見ると、DR方法の不適・不備が65%で、検図時の不適・不備が35%です。DR方法の 不適・不備65%の中味は、DR時の直接手戻り12%、出荷前立会時の手戻りは8%、 納品・検収後客先 からのクレームに伴う手戻りは45%です。 DR方法の不適・不備とは、商品・製品企画時、構想・計画図作成時、基本設計時の基本仕様設定と故障 解析と裏付け検証等の事前指導不備と欠如の結果です。これに対し検図時の不適・不備とは、詳細設計・ 製図時の担当者製造知識と注意力不足および上司・先輩の事前指導不足の結果です。検図時の不適・不備 35%の中味は、検図時の直接手戻り12%、出図後の製造と取引先からの手戻りは23%です。 そこで、DRをクレームの予防と手戻り削減として機能させるために必要な開発・設計時の評価・判定・検証法の 原則・基準・ルール・ツールを明確にし、ラインアップ、発生クレーム対策の視点をどのように活用するかを 分かりやすく紹介するセミナーを企画いたしました。また開発・設計部門以外の生産準備に携わる生産技術 部門、調達・購買部門、製造部門、品質保証部門、アフターサービス部門、営業部門、商品企画部門、販売 代理店部門等の関係者が、開発段階や設計段階での設計審査(DR)にどう関わるべきか?についても、今回 併せてご紹介致します。 前述問題点を含むクレーム防止に必要なDR方法と効果的な取り組み方法について、講師の豊富な体験を 基に具体的な対応方法をクレーム防止に役立つDRツールとして基本仕様書(DFS=Design Fundamental’s Specification)や故障解析表(FMEA=Failure Mode & Effect Analysis)等を活用する作成演習を交え具体的に 解説します。他部門も含め、DRを本当に活用したいと考えておられる開発・設計部門のリーダー、管理・監督者の 方にぜひご受講いただきたいセミナーです。
プログラム
1・クレーム防止と設計審査(Design-Review=DR)
(1)商品企画とDR-0(企画審査) (2)開発とDR-1(開発審査) (3)量産設計とDR-2(設計審査) (4)生産準備とDR-3(生産準備審査) (5)ラインアップ・初期流動管理とDR-4(ラインアップ審査) (6)市場クレーム情報とDR-5(発生クレーム対応審査) (7)設計審査会とI-DR(担当部署事前内部審査) (8)クレーム防止とDRツール
2・DRの実施法
(1)機能評価とDR方法 (2)性能・特性評価とDR方法 (3)品質(信頼性=クレーム発生確率)評価とDR方法 (4)安全性評価とDR方法 (5)リサイクル性評価とDR方法 (6)省資源・エネルギー性評価とDR方法 (7)生産対応性評価とDR方法 (8)現地施工対応性評価とDR方法 (9)コスト評価とDR方法 (10)納期性評価とDR方法 (11)試験・検証性評価とDR方法 (12)危険優先(Risk Priority)度評価とDR方法
3・クレーム防止に役立つDRツール
(1)基本仕様(Design Fundamentals Specification)で目標寿命と信頼度数値設定法とDR (2)故障解析(FMEA)を利用した故障予測で加速試験検証による不具合予防対策取組法とDR (3)試験期間を10分の1、100分の1に短縮しながら実際値と整合性を確保する検証の取組法
4・クレーム防止に役立つDRツール作成法演習
(1)DRツールとして活用する製品基本仕様による寿命と信頼度の数値設定演習と個別指導 (2)DRツールとして活用する製品故障解析による故障予測と加速試験実施法設定演習と個別指導 (3)演習で作成したツール内容の紹介と講師講評
5・質疑
講師紹介
[略歴] 17年間富士重工業㈱三鷹製作所生産技術部門に勤務、専用機設計等の工場自動化業務へ従事後、 伊豫部技術士事務所を開設、現在・工場生産合理化・IE改善業務、技術開発・製品設計部門・生産技術部門 改善等のコンサルタントとして活躍中。海外企業の指導経験も豊富 (社)日本技術士会へ所属・機械部長、理事を歴任。現在(財)りそな中小企業振興財団主催「中小企業庁 長官賞新技術・新製品賞」贈賞専門審査委員 主な著書に「設計の凡ミス退治101」、「設計のムダ退治101」、「設計者の心得と実務101」、「設計の マネジメント101」、「設計の経験則101」、「設計の基本仕様51」、「設計の故障解析51」、「設計審査(DR) 支援ツール集・Ⅰ(事前審査編)」、他(何れも日刊工業新聞社刊)