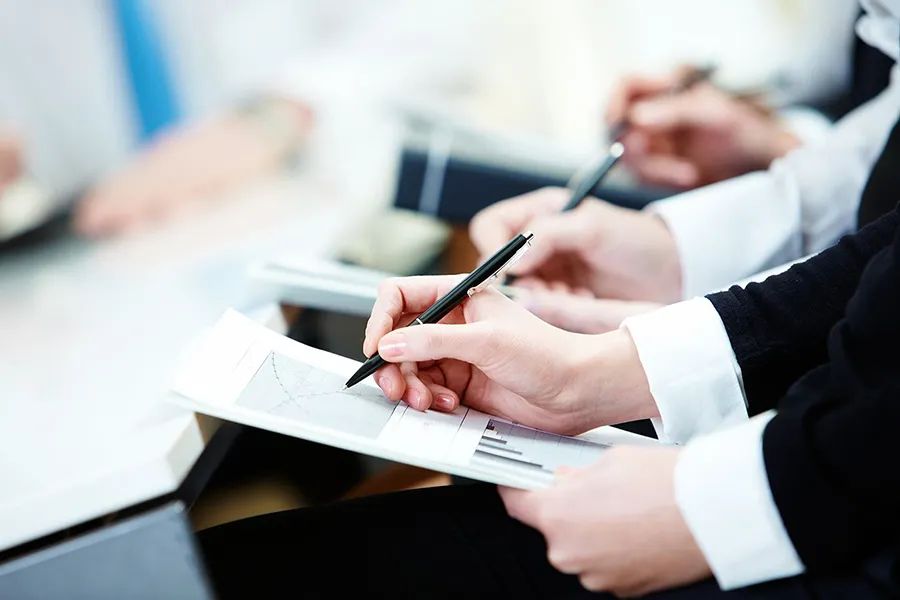
早期戦力化を図るための
ケーススタディによる若手設計者早期育成の上手な進め方
若手設計者に必要な心得と実務の原則・ルールをわかりやすく解説する特別セミナー!!
- 講師
伊豫部技術士事務所 所長 技術士(機械部門) 伊豫部 将三先生
富士重工業(株)に17年間勤務後、100社以上の各種製造企業にて開発・設計・生産部門の業務支援に従事
- 日時
- 会場
- 受講料
- 1名:47,250円 同時複数人数申込みの場合 1名:42,000円
- テキスト
受講概要
予備知識
設計部門に所属する方なら特になし
講師の言葉
あなたの所では、若手設計者の仕事に対するマナー(モラル)へ違和感を感じていませんか? 上司、先輩から テーマが与えられても、周りで総てお膳立て、準備をしてやらないと、手を着けられない。判らないことがあっても、 自分から進んで先輩や上司へ聞こうとしない。判らないことや知らないことを進んで解明、理解して、解決を 図ろうとしない。教えられるまでは、手を着けられない。毎日の目標を明確にして、その完了まで努力しない。 周囲の忙しさに関係なく時間が来れば、仕事を中断して帰宅する。また毎日の進捗状況を、自分からは先輩や 上司へ報告しない。途中で仕事の状況・進捗を尋ねられても、返事は要領を得ない。しかし都合の悪い言い訳は、 何時も周到に準備して、自分の立場はきちんと主張する。先輩・上司を尊敬しない。会議では、まだ1人前の 仕事もできない自分の立場を弁きまえずに、関係ないことに口出し発言する。 同僚・先輩の失敗を平気で 誹謗する。職場の親睦会、懇親会には、殆んど参加しない。仕事に必要な知識は、会社が就業時間内で総て 教えるのが当然だと思っている。 前述の状態は、企業規模の大・中・小に関係なく、殆んどの職場で顕著に見られる傾向です。 これら若手 設計者へ仕事に必要なマナー(モラル)を修得させるには、リーダーが系統立てきちんと心得と業務着手の原則・ ルールを指導、教育することが大切です。 本セミナーでは、まだ1人前でない5年以内の若手設計者と指導する立場にあるリーダー、管理者に対し、 必要な心得と実務の原則・ルールを、コンサルタントとして数多くの企業で若手設計者へ接し指導してきた講師が 判り易く解説、指導致します。 日頃若手設計者教育に悩んでいられるリーダー、管理者の方は、この機会に 是非ご参加を、おすすめ致します。
セミナーのポイント
1)不注意の間違い防止のルールとポイント 2)判断の間違い防止のルールとポイント 3)時間節約設計のルールとポイント 4)納期確保設計のルールとポイント 5)低コスト設計のルールとポイント 6)トラブル・クレームと設計品質のルールとポイント 7)納期確保・日程計画・進捗管理のルールとポイント 8)日常業務と標準化のルールとポイント
プログラム
1・設計担当者自身に求められる資質と心得
1-(1)上司・先輩指導受入れ法 1-(2)先輩経験・技術蓄積受入れ法 1-(3)自己啓発・技術レベルアップ法
2・品質確保につながる設計取り組み法に必要な心得と原則
2-(1)市場・客先クレーム防止に必要な設計条件・基準値設定法 2-(2)製造・ラインクレーム防止に必要な設計条件・基準値設定法 2-(3)間違いによる図書差し替え率削減に必要な自己品質確保設計・製図法
3・期間短縮につながる設計取り組み法に必要な心得と原則
3-(1)期間短縮に必要な設定日程計画法 3-(2)日程計画立案に必要な設計工数見積り法 3-(3)工数見積りに必要な標準設計方法・標準設計手順設定法
4・時間節約につながる設計取り組み法に必要な心得と原則
4-(1)類似調査・試験・検証着手防止法 4-(2)既成品・既存技術活用法 4-(3)類似内容繰返し防止標準化推進法
5・プライスダウンにつながる設計取り組み法に必要な心得と原則
5-(1)部品点数削減設計法 5-(2)使用材料削減設計法 5-(3)新規製作部品削減設計法
6・後戻り作業削減につながる設計・製図取り組み法に必要な心得と原則
6-(1)設計条件・基準値設定間違い防止設計法 6-(2)図書記入間違い防止製図法 6-(3)調査・試験・実験結果の判定間違い防止評価法
7・外部協力者支援の活用時に必要な心得と原則
7-(1)外注設計・補助者の支援活用法 7-(2)取引先業者(vendor)支援活用法 7-(3)外注受託者能力評価必要時の対応法
8・質疑応答およびコンサルテーション
セミナーで紹介する「設計者の心得と実務 101」ケーススタディの内容
1・設計担当者自身に求められる資質と心得
(1)上司・先輩指導受入れ法 01・知らないことは上司・先輩へ尋ねてから着手する (注・知らない・裏付けもないことを勝手に判断してはならない) 02・上司の指示と意向は会社の方針と心得る (注・会社・上司の命令・指示・意向に従えない者は会社に勤務することを拒否することと同じであり許されない) 03・速さは大切、しかし正確さはもっと大切と心得る (注・早くても間違いは許されない、最初は速さより正確さを大切にする) 04・自分で確保できる品質は自分で確保する (注・自分で防げる間違いを他人に指摘されるのは担当者の恥じと心得る) 05・約束した納期はどんなことがあっても必ず守る (注・守れない納期を約束して同僚・他部署・取引先へ迷惑を掛けてはならない) (2)先輩経験・技術蓄積活用法 06・既成品・既存図書を利用する場合は事前に作成した先輩へ内容を確認する (注・既成品・既存図書の問題点・メンテナンス有無を利用前に確認する) 07・既成品・既存図書があるものはこれをできるだけ活用する (注・類似の内容へ繰返し新規着手してはならない) 08・規格・基準・指針・手引・手本図等がある場合はこれに基づき着手する (注・規格類の内容を勝手な判断で変更してはならない) 09・新しく着手作成した基準・図書類は誰れでも再利用できる様に標準図書化する (注・別の担当者が類似の内容へ繰返し新規着手せず済む様に再利用できる形態で残す) 10・新規着手では類似の既成品・既存図書がない場合のみ新規図書を作成する (注・類似の内容の既成品・既存図書があるのに繰返し新規着手してはならない) (3)自己啓発・技術レベルアップ法 11・担当テーマでは常に社内・外の第一人者を目差して知識修得に努力する (注・常に第一人者の地位を目差さなければレベルは向上しない) 12・知識は他人から習うものではなく自身で身に付けるものである (注・知識は本人が覚える気持ち・意欲を持たなければ修得できない) 13・材料は素材と熱処理後の特性の違いを知って性能を出来る丈高めて使用する (注・使用材料の性質・特性を覚えることは設計の第一歩である) 14・加工は工作法による到達精度とコストの違いを知ってコストを出来る丈安くなる様設計する (注・加工・工作法を覚えることは設計の第一歩である) 15・基準値設定では「ばらつき」の違いによる確率を知ってクレームを出来る丈低めて設計する (注・確率・統計の考え方を知ることは設計の第一歩である)
2・品質確保に継がる設計取組み法に必要な心得と原則
(1)市場・客先クレーム防止に必要な設計条件・基準値設定法 16・基準値(=保証値)は使用材料の機能限界値(=試験検証値)を確認し適切に余裕(マージン)を加味して設定する (注・負荷条件が機能限界値を越えるとクレームが急激に多発する) 17・基準値(=保証値)は性能値と一緒に品質値(=クレーム発生確率値)で設定する (注・品質値を設定するとはクレームの発生確率値を管理することである) 18・製品の耐久性保証では無償保証期間(注・1年の場合24h/日×365日/年=8760h/年)連続使用に耐える確認試験を最低クリア させる (注・2年保証では17520h、3年保証では26280h、5年保証では43800h、10年保証では87600hの耐久性有無を確認する) 19・耐久性確認では促進試験(または加速試験・短縮試験)で試験期間を10分の1以下へ圧縮する (注・促進試験で10分の1へ圧縮とは1年分を37日へ短縮して試験することを言う) 20・促進試験では環境温度上昇・負荷条件の加重を組み合わせ短縮する (注・一般樹脂材料では10度C温度上昇で寿命は半減する、炭素鋼では負荷条件を15%加重すると疲労破壊までの回数は10分の1へ 減少する) (2)製造・ラインクレーム防止に必要な設計条件・基準値設定法 21・材料は工作限界を越えると加工不良となり品質クレームとなる (注・工作法と材料の組合せで工作限界に違いがあることを知り製造クレームにならない設計をする) 22・設備では加工限界を越えると製造ができず製造クレームとなる (注・保有設備の選択で加工限界・加工可能範囲・到達精度可能範囲に違いがあることを知り製造クレームにならない設計をする) 23・品質過剰(必要以上に精度を高め)にするとコストアップの要因となる (注・精度要求を必要以上高めに設定すると加工の工程数が増えることを知りコストアップにならない設計をする) 24・加工精度を高め工程数が増えると加工工数が増えコストアップの要因となる (注・加工工数が増加するとコストが増えることを知りコストアップにならない設計をする) 25・少量生産品で工程数が多く段取り替えが増えるとコストアップの要因となる (注・段取り替えが増えると工数が増加することを知りコストアップにならない設計をする) (3)間違いによる図書差し替え率削減に必要な自己品質確保設計・製図法 26・図書作成では本番の前に下書き(素案)を作り先輩・上司の点検を受けてから本番へ移行・着手する (注・いきなり図書を完成してから先輩・上司へ点検を依頼してはならない。修正・訂正・遣り直しが必要な時の後戻りの負担は 大きくなる) 27・図書作成では下書き・本番時共ツール(規格・基準・指針・手引き・手本図・既成品図書等の事例)を事前に準備してこれを 確認しながら着手する (注・判っている積りでも曖昧な記憶に頼らず面倒でもその都度の確認を繰り返す) 28・作成中の図書とツール間の点検確認では面倒でもその都度その場で指差し照合と「OK」の場合には双方を塗りつぶす (注・図書とツールの双方を塗りつぶしながら大丈夫かどうかを確信する) 29・図書作成中は取組み中のこと以外は考えず気持ちを図書へ集中させる (注・図書作成中同時に別のことを考え気持ちが分散すると手が遅くなるだけでなく間違いにも気付かない) 30・図書完成後提出前に気分を転換(気持ちを一新)し最低1回以上全体を見直す (注・気分を一新し冷静になると夢中の時は気付かない間違いが良く見える)
3・期間短縮に継がる設計取組み法に必要な心得と原則
(1)期間短縮に必要な設計日程計画法 31・所要期間短縮では所要工数削減が第一条件である (注・所要工数削減では新規着手箇所・範囲を出来る丈減らすことである) 32・所要工数削減では既成品・既存図書を最大限に活用する (注・新規着手部分を減らすには可能な限り徹底して既成品・既存図書をそのままの形で活用する) 33・開発が伴う設計では原理試作・方式試作・構造試作・生産試作(製品見本試作)の4段階試験確認が避けられないことを知り所要 工数から所要期間を見積る (注・経験がない部分の開発では原理試作・方式試作・構造試作・生産試作の途中を省略すると製品化してから市場クレームの形で 省略した部分の遣り直しが多発する) 34・納期が予め決められた設計では並行処理できる所は並列化して短縮する (注・予め決められた期間内に社内でできない場合は並行処理アルゴリズムの原理を応用し外部支援も活用し複数人の同時並列処理 で短縮する) 35・所要期間短縮では試作品試験の際、見込みのない案は早く捨てる決断が大切 (注・試験データがだめでも改良で良くなるかも知れないと判断し引きずると所要期間が際限もなく延長する原因となる) (2)日程計画立案に必要な設計工数見積り法 36・所要工数見積りはやらなければいけないことは総て事前に摘出して着手する (注・当初の着手範囲を最少限に絞り込むと後から追加・修正が多発し、実績工数が見積り工数を大幅に超過し納期遅れの繰返しと なる) 37・所要工数の見積りは着手テーマの基本仕様をきちんと整理してから着手する (注・基本仕様が曖昧では着手すべきこと不要なことが曖昧となり所要工数も見積れない) 38・所要工数の見積りは最初にテーマと内容毎に標準設計方法・標準設計手順を定め誰れが着手しても所要時間をきちんと読める様に する (注・誰れが担当するかで着手方法・手順が変わっては所要時間が一定しない、つまり見積りは困難となる) 39・所要時間の見積りでは勤務時間を100%設計時間へ置換えてはならない (注・勤務時間中に占める実設計投入可能時間は平均20%以下が実態である) 40・所要時間の見積りでは正味設計時間と付帯技術雑務の比率を事前に把握する (注・所要時間の見積りでは勤務時間の50%以上が技術雑務で費やされている実態がある) (3)工数見積りに必要な標準設計方法・標準設計手順設定法 41・標準開発時間設定に必要な標準開発方法・標準開発手順設定では経験ある先輩・ベテランが抜けのない様に作成する (注・標準開発時間設定の標準開発方法・標準開発手順作成では誰れがやってもできるレベルに方法・手順を分解して示す) 42・標準設計時間設定に必要な標準設計方法・標準設計手順設定では経験ある先輩・ベテランが抜けのない様に作成する (注・標準設計時間設定の標準設計方法・標準設計手順作成では誰れがやってもできるレベルに方法・手順を分解して示す) 43・標準製図時間設定に必要な標準製図方法・標準製図手順設定では経験ある先輩・ベテランが抜けのない様に作成する (注・標準製図時間設定の標準製図方法・標準製図手順作成では誰れがやってもできるレベルに方法・手順を分解して示す) 44・標準検図時間設定に必要な標準検図方法・標準検図手順設定では経験ある先輩・ベテランが抜けのない様に作成する (注・標準検図時間設定の標準検図方法・標準検図手順作成では誰れがやってもできるレベルに方法・手順を分解して示す) 45・標準開発時間・標準設計時間・標準製図時間・標準検図時間等の所要時間設定では新人等が実際に取組んだ結果の実時間を基礎に 設定する (注・標準所要時間設定は何人かで実施し間違いなく早くできた人の時間を基準とする。平均時間を標準所要時間にしてはならない)
4・時間節約に継がる設計取組み法に必要な心得と原則
(1)類似調査・試験・検証着手防止法 46・開発時のアイデアは自身で考えるな、出来る丈他人のアイデアを活用する (注・特許は同じ悩みに遭遇した先人が考えたアイデアの宝庫これを最大限利用する) 47・アイデアが使い物になるかどうかの判定は試作・試験・実証して評価する (注・図や説明文のみで善し悪しを判断しない実証して判定する) 48・試作品の評価法と判定基準は試験着手前に設定する (注・評価法と判定基準なしの試験実施はだめなものを何時までも追い駆ける結果となる) 49・評価して一定の基準を満たさないアイデアは早く捨て別なアイデアを試験する (注・当初アイデアを多数用意しその中から1つ使えるものを残す考え方で試作・試験する) 50・一度試験したアイデアはデータを後へ残し同じアイデアは繰返し試験しない (注・データが残っていれば同じアイデアを試験する繰返しが省ける) (2)既成品・既存技術活用法 51・既成品はできるだけ手を加えずにそのまま活用する (注・既成品は市場で耐久性や信頼性で一定の評価を獲得していることに着目する) 52・既成図書はできるだけ手を加えずにそのまま活用する (注・既成図書による製品は製造や客先で耐久性と信頼性で一定の評価を獲得していることに着目する) 53・要求仕様を満たしコストの安いものは社内・外を問わず取り入れ活用する (注・新規設計・製作が避けられるものは出来る丈これを活用する) 54・市販量産規格品を新たに採用する場合にはメーカーへ耐久性・信頼性データを要求する (注・市販量産規格品を新たに採用では当初性能の確認だけでなく耐久性・信頼性も確認してから採否の評価をする) 55・市販量産規格品を新たに採用する場合には並行して社内でも耐久性・信頼性試験を行い採否の評価をする (注・メーカーだけのデータを鵜呑みにしない自身でもきちんと確認する) (3)類似内容繰返し防止標準化推進法 56・新規に作成する図書は総て標準図化する (注・一度作成した図書は標準図化しデータベース化して何時でも誰れでも直ぐ検索・活用できる様にする) 57・新規テーマへ着手する場合には品質機能展開表(QFD)の形態で標準仕様書をその都度作成しデータベース化する (注・Iyobe式Formatによる品質機能展開表で標準仕様書を作成し仕様書のデータベース化を進めその都度の類似仕様書作成 繰返しを防止する) 58・類似テーマへ着手する場合には既成品の標準仕様書と異なる箇所のみを設計上の管理対象とする (注・標準仕様書が既に存在する場合には異なる箇所と同じで済む所をきちんと明確にし着手箇所を異なる所のみに限定・制限する) 59・新規テーマへ着手する場合でも事前の設計審査(Design Review)で新規着手可能範囲を確認する (注・新規テーマでも総てを新規に着手することは出来る丈避ける。着手して良い範囲は出来る丈絞り込む) 60・担当者が着手する前に既成品・既存図書活用と新規着手設計製作可能範囲の目標構成比率ガイドラインを明確にする (注・構成部品数に占める既成品・既存図書活用比率と新規設計製作品比率に目標ガイドラインを設定しこの実現に努力する)
5・プライスダウンに継がる設計取組み法に必要な心得と原則
(1)部品点数削減設計法 61・複雑形状品では出来る丈型成形品(鋳造・ダイカスト・プレス・インジェクション等)化する (注・型成形化で部品点数を削減する) 62・型成形化できない場合には溶接・接着を出来る丈活用する (注・溶接・接着で部品点数は減らないが加工箇所を削減する) 63・ねじ締結法は出来る丈避ける (注・ねじ締結は部品点数増加・加工箇所増加・組立て箇所増加に継がる) 64・切削加工が伴う部品構成法は出来る丈避ける (注・切削加工箇所が多いと工数増加・コスト増加の要因となる) 65・組立て時に調整が伴う部品構成法は出来る丈避ける (注・組立て時に調整箇所が有ると工数増加・コスト増加の要因となる) (2)使用材料削減設計法 66・炭素鋼材等の金属材料は熱処理で強度性能を高めて使用する (注・熱処理をしない素材のままでは高級材料も強度性能がでない) 67・同じ材種でも合金成分の「バラツキ」が少ないメーカーの材料を使用する (注・JIS番号が同じ材種でもメーカー毎に「バラツキ値」が異なることに着目する) 68・同じ材料でも熱処理等製造時の作業法の違いによる「バラツキ」に注意する (注・使用設備の違いによる「バラツキ」や作業者の違いによる「バラツキ」に注意を払い、「バラツキ」の少ない作業法を 設計上で指定する) 69・安全率は品質値(クレーム発生確率値)で置換える (注・材料強度の「バラツキ」は品質値を管理しない場合にクレームの発生確率へ影響することに注意する) 70・強度性能に対する保証は安全率設計でなく確率設計で設定する (注・安全率設計では「バラツキ」の変化でクレームになる場合もあることに注意する) (3)新規製作部品削減設計法 71・市販量産規格品で適用出来るものは無条件でこれを採用する (注・新規製作品は市販量産品よりコストが高くなることに注意を払う) 72・市販品採用で競合メーカーがある場合には相見積りで安い側を選択する (注・競合メーカーがあるものは性能・品質が良く安いものを選択する) 73・市場でライバル関係でも自社製作品より安く受給可能なものは無条件でこれを採用する (注・ライバル企業の部品でもOEM委託・受給可能ならこれを受入れ活用する) 74・社内他事業部・他分野量産製品の部品で適用可能なものは無条件でこれを採用する (注・新規製作品は社内でも既存量産品よりコストが高くなることに注意を払う) 75・非量産品でも既存部品と共通化できるものは無条件でこれを適用する (注・非量産品でも既存部品と共通化することで新規製作品よりコストが安くなることに注意を払う)
6・後戻り作業削減に継がる設計・製図取組み法に必要な心得と原則
(1)設計条件・基準値設定間違い防止設計法 76・耐久性が必要なものは「引張(破断)強さ」でなく「疲れ強さ」で設計する (注・炭素鋼熱処理材の「疲れ強さ」は「引張(破断)強さ」の45%である) 77・荷重が複雑に掛る場合の材料強度は「ねじり(剪断)強さ」で設計する (注・「曲げ強さ」や「引張強さ」より「ねじり(剪断)強さ」の方が弱い) 78・疲れ強さと衝撃強さの確保も同時に必要な場合には炭素鋼では硬さをHRC40前後に設定する (注・「疲れ強さ」と「衝撃強さ」の両方を適切に確保できる硬さで設定する) 79・一般樹脂材料では雰囲気温度が10度C上昇すると寿命は半減する (注・温度上昇が寿命に強く影響する材料選択では上限温度を管理する) 80・耐寒仕様・寒冷地仕様では使用材料の衝撃強さ確保に注意する (注・耐寒仕様=-40゚C放置-20゚C使用、寒冷地仕様=-60゚C放置-40゚C使用の環境下では炭素鋼材の衝撃強さが確保できないことに 注意する) (2)図書記入間違い防止製図法 81・相互関連・組合せ・嵌合せ・取合い部分では「同時記入」する (注・関連部品同士の取合いがある部分は両方を一緒に決めることで間違いを防ぐことができる) 82・干渉防止では動作・寸法・時間等のチャート作成による「別個に点検」する (注・出図しなくても間違い防止には裏付けの図書作成を習慣化する) 83・手計算では「1桁毎の逆算・検算」が原則である (注・手計算では答え合せに通し算の繰返しを止め面倒で遅くても1桁毎の逆算・検算により1回で終了する習慣とする) 84・部品点数等の拾い出しでは、「通し」で数えず「小グループ」毎に積上げる (注・数量が多い部品点数を「通し」で数えると「抜け」・「ダフリ」で間違うことに注意する) 85・記入間違い防止ではその都度その場で指差し照合による見直し確認を積上げる (注・後でまとめて間違い有無を点検するのではなく、何時もその都度その場で間違いがない様に確信を積上げる様習慣化する) (3)調査・試験・実験結果の判定間違い防止評価法 86・試験では「OK」・「NO」の判定基準を予め決めてから開始する (注・成り行きで試験を行なってはならない) 87・試験法はデータの「ばらつき」をきちんと把握する (注・サンプル数は「ばらつき」を把握できる数を準備する) 88・試験法はデータの「傾向」が読める条件で設定する (注・負荷条件は最低3以上条件を変えて設定する) 89・サンプル数は「ばらつき」と「傾向」の両方が同時に判る条件で設定する (注・負荷条件の違う各々で的確にばらつきを把握できる数を準備する) 90・試作・試験は正しい設計値を決めるために「機能限界値」を把握するのが目的 (注・データから機能限界値=-3σ位置が何処にあるか最初に確認する)
7・外部協力者支援の活用時に必要な心得と原則
(1)外注設計・補助者の支援活用法 91・外注設計の委託契約では委託範囲・内容・条件・納期・検収条件を当初きちんと取り決める (注・特に受託者の手直しが必要時の遣り直し方法と検収方法の取決めを忘れない) 92・外注設計の委託契約では間違いに対するペナルティを取り決める (注・検収後受託者の間違いによる損害発生時の補償・ペナルティはきちんと取り決める) 93・持帰り設計委託では進捗の定期的連絡を義務付ける (注・納期が近付き遅れ回復できない状態で遅延が判明する等のない様、最低毎週の進捗報告を義務付ける) 94・構内派遣者への設計委託では帰宅前毎日の進捗報告を義務付ける (注・その日完了した作業部分と翌日の取組み予定作業内容を報告してから帰宅する様、当初契約で義務付け毎日の進捗状況を 把握する) 95・派遣のCADオペレータへの図書作成委託ではその都度・その場の自己点検・確認を義務付ける (注・本人で防げる間違いはその都度・その場で本人へ防止させる習慣を当初の契約で義務付け守らせる) (2)取引先業者(vendor)支援活用法 96・外部業者委託では当初の「基本仕様取決め」が総てである (注・外部委託では要求仕様が不明確の状態で発注してはならない) 97・業者提出図書の承認基準は要求の基本仕様充足が最低条件である (注・検収のための承認手続きは最低限要求の基本仕様を満たしていること) 98・検収は業者に対する最終の受入れ承認である (注・間違いがある場合には検収後も手直しを条件に当初契約の上承認する) 99・受入れ後の不具合は速やかに受託者へ改善の対応を要求する (注・間違いや不具合は発見次第速やかに修正実施の対応を要求する) 100・発注仕様の変更は委託条件(費用=工数・納期=期間)の変更である (注・発注後の仕様変更は出来る丈避ける、避けられない場合には当初見積りの範囲で可能かどうかで対応する) (3)外注受託者能力評価必要時の対応法 101・受託者の能力評価は委託テーマの所要時間・消化量・金額・間違い発生件数・不具合時の対応力等のデータで比較する (注・月当りの投入時間・消化件数量・金額・間違い発生件数・不具合時の対応程度を毎月集計し、受託者間で比較する)
講師紹介
富士重工(株)三鷹製作所生産技術部に17年間勤務。主として専用機設計等の工場自動化業務に従事。 その後,技術士事務所を開設。 現在開発・製品設計および生産技術部門のコンサルタントとして材料使用量削減による製品コストダウン、故障 解析による加速試験と事前検証法導入でクレーム削減、手戻り削減になる欠陥・不備・間違いを最初から入れない 途中で作り込まない、後から出さない設計の仕組み構築の効率向上指導等で活躍中。 関与した企業数は国内大手および中堅企業で既に100社を越える実績を持つ。 他に韓国、台湾企業の海外指導経験も豊富。 (社)日本技術士会・理事・機械部会長を歴任。 りそな振興財団と日刊工業新聞社主催「新製品・新技術中小企業長官賞」専門審査委員、等を歴任。 分かり易く,豊富な事例で進める指導法には定評がある。 ■主たる著書: 「設計の経験則101」、「設計者の心得と実務101」、「設計のマネジメント101」、「設計のムダ退治101」、 「設計の凡ミス退治101」、「設計の基本仕様51」、「設計の故障解析51」、「ハンドリング自動化201」、 「設計審査支援ツール集・Ⅰ(事前審査編)」「検図に関する100のアドバイス」月刊「機械設計」誌面に36回 連載、「設計力向上のアドバイス」 月刊「機械設計」誌面に51回連載。 以上は日刊工業新聞社から刊行。「品質機能展開(QFD)表事例集」、 「組付・ハンドリング自動化実例図集(熊谷卓氏と共著)」、以上は新技術開発センターから刊行、等。